Managing Materials
This section provides an overview on material management transactions and modify ship to addresses.
Page Name |
Definition Name |
Usage |
---|---|---|
RF_MATERIAL_ORDERS |
Request materials that are required to perform a service order activity. There is a second Order Materials component with the same navigation and object name. This component is security-based in that it only retrieves service orders that are assigned to the user who signed into the system. It is similar to My Service Order. This page is the same as the regular Order Materials page, except it returns different search results. |
|
RF_MANAGE_MAT_ADD |
View and modify the address where the material that is ordered on the Order Materials page will be shipped. |
This section discusses:
Item balances.
Item availability.
Material orders.
Requisition status.
Receipts of material.
Item Balances
Before ordering an item for a service order activity on the Order Materials page, you can check item balance information at two levels:
Stock balances for the good truck stock storage locations that have been associated with each member of the provider group assigned to the service order line.
The current quantity that is available and on-hand balances for the inventory business units that form the distribution network for your field service operations.
With this information, you can determine whether a material order is necessary and, if so, set expectations about when material will be received based on whether the required quantity is stocked in one of your distribution centers or must be ordered from an external vendor.
In PeopleSoft CRM, group members are associated with storage locations in your inventory system that represent their good and defective truck stock. You make these associations on the Storage Locations page of the Worker component. The PeopleSoft CRM system uses the Item Balance EIP to retrieve balance information for the good truck stock storage locations from PeopleSoft Inventory or your third-party inventory system. The balance information appears on the Item Balance by Group Members page in PeopleSoft CRM.
Image: Integration that supports balance checking for truck storage locations
This diagram illustrates how the integration between PeopleSoft CRM and your inventory system supports storage location balance checking.
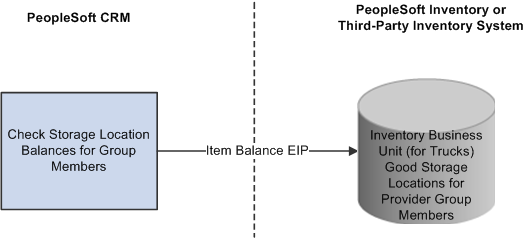
You can also check on-hand balances for the inventory business units included in the distribution network defined for your field service operations. The PeopleSoft CRM system uses the Item Balance EIP to retrieve the quantity that is available and on-hand balance information from the appropriate inventory business units defined in PeopleSoft Inventory or your third-party inventory system. The balance information appears on the Item Balance by Business Units page in PeopleSoft CRM.
Note: When integrating with PeopleSoft Purchasing and PeopleSoft Inventory, you define a distribution network of inventory business units for each business unit in PeopleSoft CRM that can request material for service orders or as replacements or exchanges for material returns.
Image: Integration that supports checking the quantity that is available and on hand
This diagram illustrates how the integration between the PeopleSoft CRM system and your inventory and purchasing systems supports on-hand balance checking.
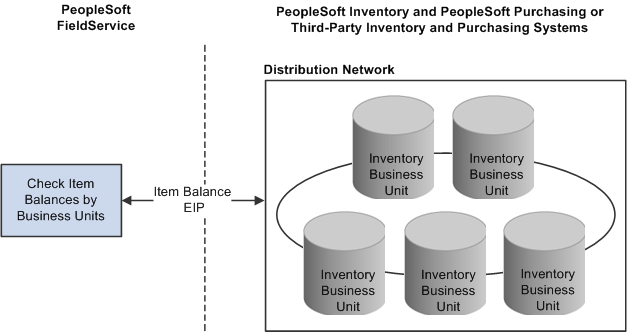
Item Availability
If your PeopleSoft CRM system is integrated with PeopleSoft Inventory and you are accessing system pages through the portal by using the single sign-on feature, you can access the Item/Product Availability component in PeopleSoft Inventory from the Order Materials page.
With the Item/Product Availability component, you can confirm the current quantity that is available for an item, check the cumulative available-to-promise (ATP) quantity for future dates, and view future supply and demand information for the item.
This information enables you to set expectations about the expected receipt date for items that are being ordered to complete work on a service order line or to replace material that a customer is returning. This functionality is especially useful for items that are currently out of stock or for which demand often exceeds supply.
Order Materials
When you click the Order and Receive Items button on the Order Materials page after ordering material, the PeopleSoft CRM system stages a requisition for the order quantity in PeopleSoft Purchasing or your third-party system by using the Purchase Order Requisition EIP.
If your implementation includes PeopleSoft Purchasing and PeopleSoft Inventory, sourcing processes in PeopleSoft Purchasing determine whether the order can be partially or completely fulfilled by an interunit transfer from the inventory business units in your distribution network or whether a purchase order must be placed with an external vendor.
The appropriate interunit transfer orders and purchase orders are created in the applicable systems, fulfilled by the inventory business unit or vendor, and shipped to the address specified for the material line in PeopleSoft CRM.
Note: In PeopleSoft CRM, interunit transfers are stock transfers between inventory business units in the enterprise. One of the assumptions of the integration design that supports material orders for service order lines is that material is transferred from an inventory business unit to the inventory business unit in which the technician's good truck stock storage location is defined.
For this reason, we recommend that you define an inventory business unit to track only truck stock storage locations. To prevent stock in the truck storage locations from being used to fulfill other material requests, the inventory business unit for trucks should not be included in any distribution networks defined in PeopleSoft Purchasing.
Image: Integration that supports ordering required material
This diagram illustrates how the integration between the PeopleSoft CRM system and your inventory and purchasing systems supports ordering the material that is required to complete work on a service order activity.
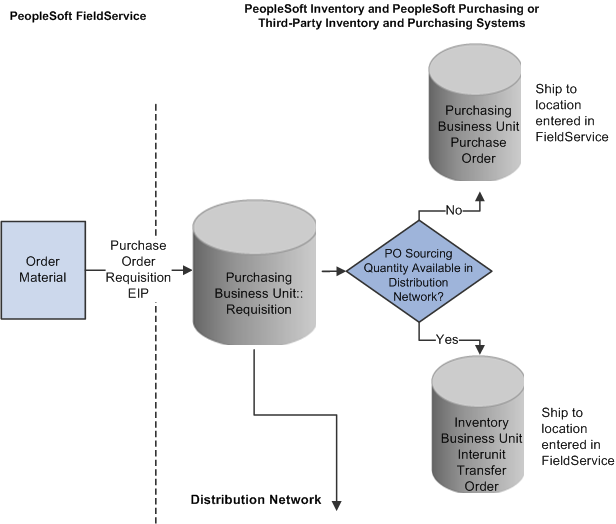
Note: PeopleSoft Purchasing or your third-party purchasing system handles processing of the requisitions that are staged by the Purchase Order Requisition EIP. In your purchasing system, you must set processing defaults for the staged requisitions and perform any required actions to complete the ordering process.
Requisition Status
In implementations that include PeopleSoft Purchasing on the portal, you can transfer to the Requisition Workbench in PeopleSoft Purchasing to check the processing status of orders that are initiated from the Order Materials page.
When an order is initiated from the Order Materials page, the system stages a requisition for the order in PeopleSoft Purchasing by using the Purchase Order Requisition EIP and displays the requisition ID that is assigned to the order on the material line.
By using the requisition ID as search criteria for the Requisition Workbench, you can check the status of the requisition in PeopleSoft Purchasing. The Requisition Workbench also enables you to check the status of all requisitions by the requester that are listed on the material line.
Note: In PeopleSoft CRM, you can define a default requester ID on the User Preferences - Overall Preferences page under If your system integrates with PeopleSoft Purchasing, the requester ID on the requisition must be a valid user ID and requisition requester in PeopleSoft Purchasing.
Receiving Material
When defining a field service business unit on the FieldService Definition page, you can determine whether the material orders that are initiated from the Order Materials page can be automatically received. The item ID is populated with the ordered item ID. If a substitute item was received instead, the user must enter the substitute item ID.
With automatic receiving, technicians enter usage information only in the service order component, not the order materials component, from which the system automatically derives and posts the appropriate receiving transactions.
If automatic receiving is not enabled, technicians manually record receipt of ordered material in the Receipts grid on the Order Materials page. The PeopleSoft CRM system uses the Get PO IUT EIP to retrieve expected receipt information for any purchase orders or interunit transfer orders that are created in your inventory and purchasing systems to fulfill the requested quantity on the item line.
Image: Integration that supports retrieving expected receipt information
This diagram illustrates how the integration between the PeopleSoft CRM system and your inventory and purchasing system supports retrieving expected receipt information.
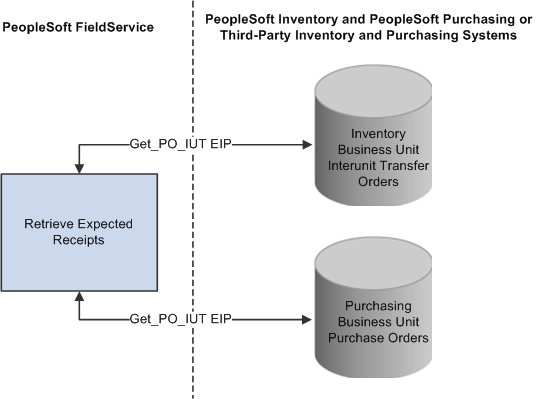
You can modify the expected receipt information to reflect the actual material shipment. When you click the Order and Receive Items button on the Order Materials page, the PeopleSoft CRM system stages the appropriate receipt transactions in your purchasing and inventory systems by using the PO Receipt EIP for purchase orders and the Interunit Receipt EIP for interunit transfers.
Note: When you record the receipt of ordered materials, you can choose the receiving technician from a list of all technicians assigned to the service order. On the PeopleSoft SCM side, the system calculates receipts against either the interunit transfers or purchase order for the good storage location of the technician who received the materials. If automatic receiving is enabled, then the used and not used material transactions are used to calculate the receipt quantity. This calculation is made against the good storage location of the selected technician instead of the lead technician’s good storage location.
Both interunit and purchasing receipt transactions are staged to your inventory system so that the quantity in the storage location that is associated with the lead technician's good truck stock can be increased by the receipt quantity. If your system integrates with PeopleSoft Inventory, the system increases the quantity in the corresponding storage location when the Putaway process is run for the receipt.
Important! When integrating with PeopleSoft Inventory, you must clear the Flag Items for Auto-Putaway check box to require a receipt transaction to be performed against all interunit receipts. When the Flag Items for Auto-Putaway check box is selected, the PeopleSoft Inventory system automatically sets the status of the interunit transfer to Received without requiring a receipt transaction. If the status of the receipt is set to Received, the PeopleSoft CRM system cannot retrieve the expected receipt information for the order on the Order Materials page.
Image: Integration that supports recording the receipt of material shipments
This diagram illustrates how the integration between the PeopleSoft CRM system and your inventory system supports recording the receipt of material shipments that are ordered to complete work on a service order line.
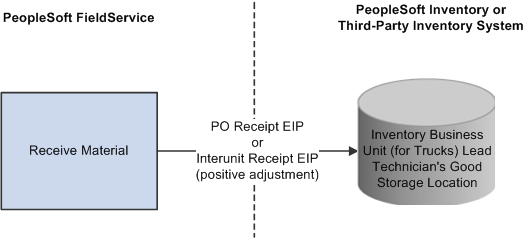
For more information, refer to the following documentation:
PeopleSoft Inventory
PeopleSoft Purchasing
Use the Order Materials page (RF_MATERIAL_ORDERS) to request materials that are required to perform a service order activity.
Navigation
Image: Order Materials page
This example illustrates the fields and controls on the Order Materials page.
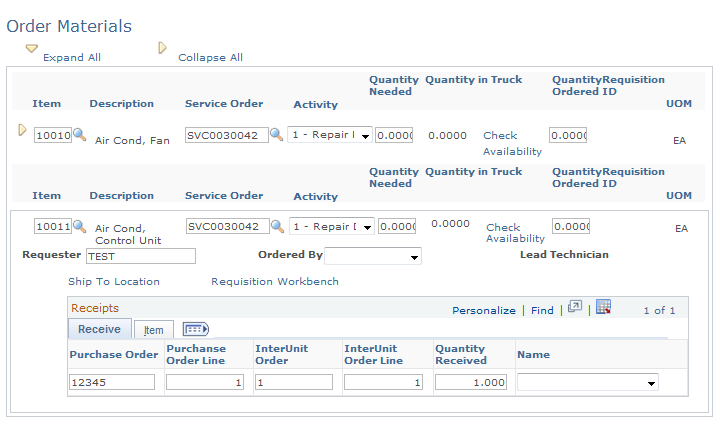
If the service is defined with service activities, the system populates the material orders record with the material that is defined for the service activities. If no activities are defined for the service, the system populates the manage material record with the material that is defined for the service. Each item defined for the service or service activity becomes a material line on the material orders record. Click the Add Needed Item button at the bottom of the page to insert additional material line rows.
Note: Unless overridden by the requester, materials are shipped to the technician specified on the material line on the service order.
This information appears for each item:
Field or Control |
Definition |
---|---|
Item |
Displays the item required to perform the service activity. The system displays the description of the selected item next to this field. Items are established in your system tables by using the Item Definition page or the Item Master EIP. |
Service Order |
Displays the service order number. |
Activity |
Displays a description of the activity. |
Quantity Needed |
Displays the amount of the item, in the item's standard unit of measure, that is required to perform the service or service activity as defined in the Service component. |
Quantity in Truck |
Displays the amount of the item that is in the technician's truck. This field is populated with the results of the Item Balance by Group Member EIP. |
Check Availability |
Click this link to access a transfer page with the these links:
|
Quantity Ordered |
Displays the amount of the item that was ordered. |
UOM (unit of measure) |
Displays the standard unit of measure for the item quantity. |
Item Details
Field or Control |
Definition |
---|---|
Requester |
Enter the ID of the person or entity associated with the requisition request. The system populates this value with the default requester ID defined on the User Preferences - Overall Preferences page. If you have implemented PeopleSoft Purchasing, you can use the requester ID and the Requisition Workbench to check the status of all the requisitions that are entered by a specific person. Important! If your system integrates with PeopleSoft Purchasing, the requester ID must be a valid user ID and requisition requester in PeopleSoft Purchasing. Requesters are established under in PeopleSoft Supply Chain Management. |
Ordered By |
Select the name of the person who is ordering the item. |
Lead Technician |
Displays the name of the lead technician for the service order activity. |
Ship To Location |
Click this link to access the Material - Ship to Address page, where you can view and modify the address where the ordered material will be shipped. By default, the PeopleSoft CRM system populates the ship to location with the address that is associated with the lead technician's location code, as selected on the Job Detail page of the Worker component. Locations are defined under Note: After you click the Order and Receive Items button, you cannot modify the ship to address in your PeopleSoft CRM system. After the Purchase Order Requisition EIP has been published, you can change the ship to address only in your purchasing or inventory systems. |
Requisition Workbench |
If the implementation includes PeopleSoft Purchasing, you can click this link to check the requisition status by requester or requisition. |
Receipts
Enter receiving information when automatic receiving is not selected at the business unit level. When automatic receiving is selected, the system hides this grid. Users can enter an amount in the Quantity Received field. To enter a substitute item, serial ID, and lot ID, select the Item tab.
After entering receipt data, click the Order and Receive Items button at the bottom of the page to save the information. The system then runs the PO Receipt and Interunit Receipt EIPs.
Field or Control |
Definition |
---|---|
Order and Receive Items |
Click to save the page and create a requisition for the order quantity in PeopleSoft Purchasing or your third-party system. Note: The label on the Order and Receive button changes to Order when automatic receiving is enabled. |
Add Needed Items |
Click to add a new item to a service order. The system displays a new grid that you can use to add a new item to the order. |
Use the Material - Ship to Address page (RF_MANAGE_MAT_ADD) to view and modify the address where the material that is ordered on the Order Materials page will be shipped.
Navigation
Click the Ship To Location link on the Order Materials page.
Image: Material - Ship to Address page
This example illustrates the fields and controls on the Material - Ship to Address page.
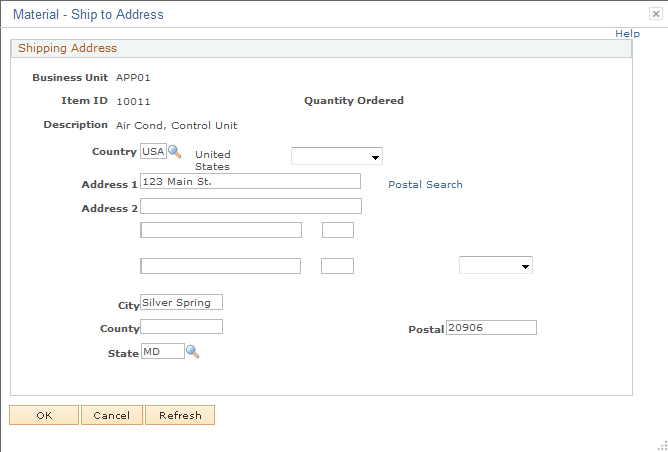
You can modify the ship to address information for each material line on the Order Materials page until the quantity is ordered for the line. After you enter an order quantity on the material line and click the Order and Receive Items button on the Order Materials page, the ship to address information can be viewed only, not updated.