6 Assemblies
6.1 Intra-system Cable Installation
This section covers the installation of cables that run within frames and between frames in a multiple frame installation. The cables covered in this section have been connected at one end in the factory and have connectors and are labeled at the other end for ease of installation. Consult the Equipment Specification for this installation and the label at the unconnected end of each cable to determine its connection point.
warning:
The intra-building port(s) of the equipment or subassembly is suitable for connection to intra-building or unexposed wiring or cabling only. The intra-building port(s) of the equipment or subassembly MUST NOT be metallically connected to interfaces that connect to the Outside Plant (OSP) or its wiring. These interfaces are designed for use as intra-building interfaces only (Type 2 or Type 4 ports as described in GR-1089-CORE, Issue 4) and require isolation from the exposed OSP cabling. The addition of Primary Protectors is not sufficient protection in order to connect these interfaces metallically to OSP wiring.The cables covered in this section are:
For additional information concerning cables and cable replacement, see Cables and Adapters.
Recommended Tools
Oracle tools should be labeled “Property of ORACLE” with either a press-on Field Tool Identification label or Field Tool Identification wrap.
-
Safety glasses
-
Tie-wrap tool
-
Flush cutters
-
Slotted screwdriver, 1/8-inch blade with 8-inch shank preferred
-
Phillips screwdrivers #2 and #3
-
Wrist strap
6.1.1 Install IMT Cables
The Interprocessor Message Transport (IMT) cables are specific lengths, based on their application. Termination information is furnished on the cable labels. Refer to Cables and Adapters and Part Numbers
danger:
Always wear a wrist strap or other electrostatic protection when handling printed circuit cards and other electrostatic-sensitive devices.6.1.1.1 Rack Alarm and Row Alarm Cable Routing
The rack alarm cable leads from ports in the control backplane and connects up to six frames in the row. See Figure 6-4 and A Clock and B Clock Cable Replacement.
The row alarm cable leads from J34 on backplane 850-0330-06/07 or 7333412 on the control shelf backplane and terminates in the control frame end panel.
Note:
The clocking and fan control signals used to support frame 6 and frame 7 are eliminated in the 850-0330-06 or -07 version and later of the Control Shelf Backplane because those frames are no longer supported in the EAGLE STP system.Figure 6-4 Control Shelf Cabling
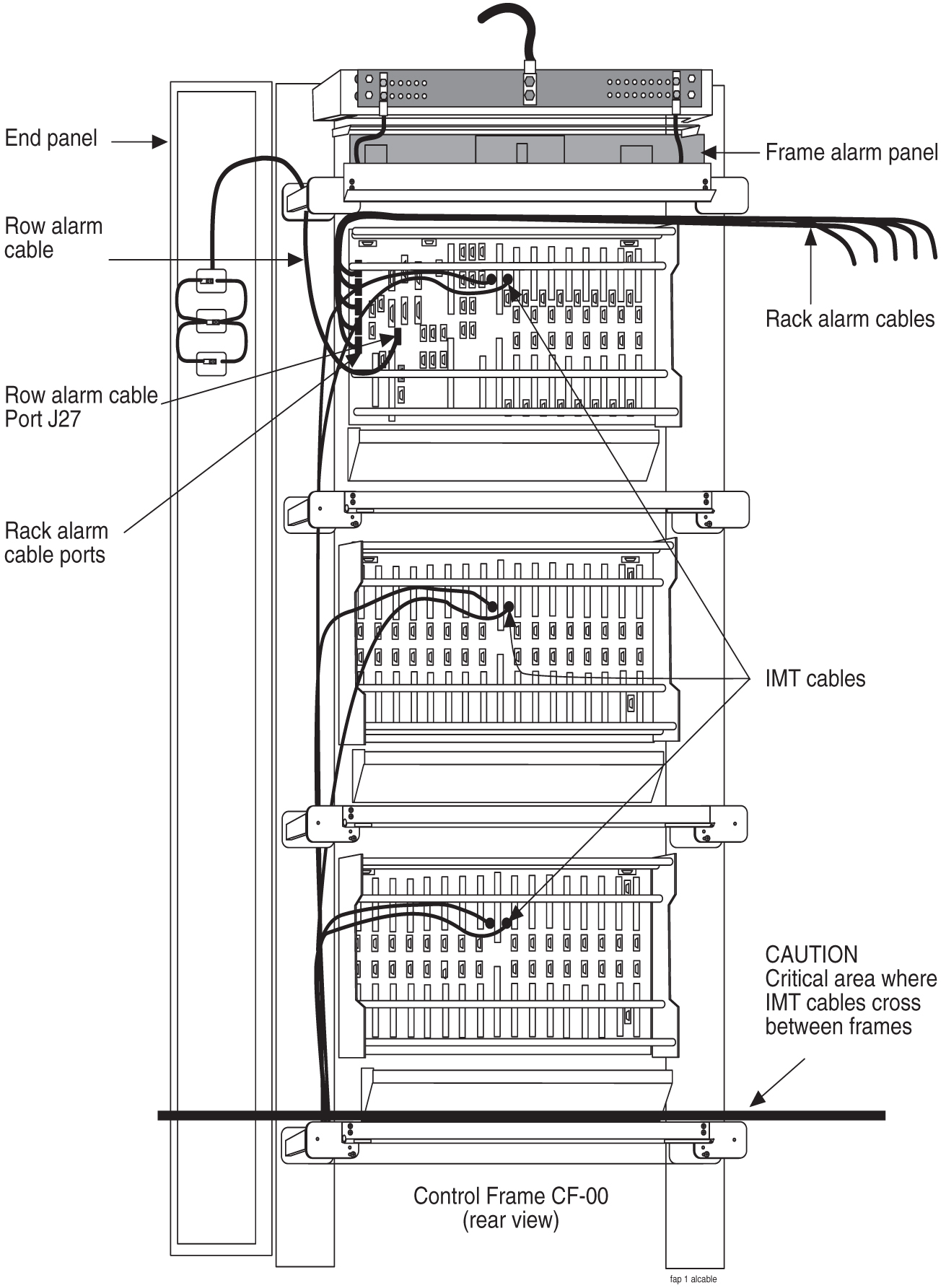
6.1.2 Interface Cable Installation
The procedure in this section is used to install the interface cables. The interface cables, one per signaling link, contain solid conductor twisted pairs for both directions of transmission in a single shield. They have connectors at one end for connection to the system backplanes.
Note:
Run Link Interface Module (LIM) cables on traverse arms, behind IMT and clock cables.The ends without connectors are normally terminated on a DSX cross-connect panel with wire-wrap terminals.
6.1.2.1 Interface Cable Installation Order
Interface cables should be installed in the following order.
6.1.2.1.1 Control Frame CF-00 Backplane
(P/N 850-0330-04/06/07) or 7333412
Control shelf 11
1101 A through 1108 A (P/N 850-0330-06 or -07 connectors J45 through J38)
1101 B through 1108 B (P/N 850-0330-06 or -07 connectors J59 through J52)
1111 A through 1112 A (P/N 850-0330-06 or -07 connectors J37 and J36)
1111 B through 1112 B (P/N 850-0330-06 or -07 connectors J51 and J50)
Extension shelf 12
1201 A through 1208 A (connectors J24 through J17)
1201 B through 1208 B (connectors J40 through J33)
1211 A through 1218 A (connectors J16 through J9)
1211 B through 1218 B (connectors J32 through J25)
Extension shelf 13 Backplane (P/N 850-0356-03)
1301 A through 1308 A (connectors J24 through J17)
1301 B through 1308 B (connectors J40 through J33)
1311 A through 1318 A (connectors J16 through J9)
1311 B through 1318 B (connectors J32 through J25)
6.1.2.1.2 Extension Frame EF-00
Extension shelf 21
2101 A through 2108 A (connectors J24 through J17)
2101 B through 2108 B (connectors J40 through J33)
2111 A through 2118 A (connectors J16 through J9)
2111 B through 2118 B (connectors J32 through J25)
Extension shelf 22
2201 A through 2208 A (connectors J24 through J17)
2201 B through 2208 B (connectors J40 through J33)
2211 A through 2218 A (connectors J16 through J9)
2211 B through 2218 B (connectors J32 through J25)
Extension shelf 23
2301 A through 2308 A (connectors J24 through J17)
2301 B through 2308 B (connectors J40 through J33)
2311 A through 2318 A (connectors J16 through J9)
2311 B through 2318 B (connectors J32 through J25)
6.1.2.1.3 Extension Frame EF-01
Extension shelf 31
3101 A through 3108 A (connectors J24 through J17)
3101 B through 3108 B (connectors J40 through J33)
3111 A through 3118 A (connectors J16 through J9)
3111 B through 3118 B (connectors J32 through J25)
Extension shelf 32
3201 A through 3208 A (connectors J24 through J17)
3201 B through 3208 B (connectors J40 through J33)
3211 A through 3218 A (connectors J16 through J9)
3211 B through 3218 B (connectors J32 through J25)
Extension shelf 33
3301 A through 3308 A (connectors J24 through J17)
3301 B through 3308 B (connectors J40 through J33)
3311 A through 3318 A (connectors J16 through J9)
3311 B through 3318 B (connectors J32 through J25)
6.1.2.1.4 Extension Frame EF-02
Extension shelf 41
4101 A through 4108 A (connectors J24 through J17)
4101 B through 4108 B (connectors J40 through J33)
4111 A through 4118 A (connectors J16 through J9)
4111 B through 4118 B (connectors J32 through J25)
Extension shelf 42
4201 A through 4208 A (connectors J24 through J17)
4201 B through 4208 B (connectors J40 through J33)
4211 A through 4218 A (connectors J16 through J9)
4211 B through 4218 B (connectors J32 through J25)
Extension shelf 43
4301 A through 4308 A (connectors J24 through J17)
4301 B through 4308 B (connectors J40 through J33)
4311 A through 4318 A (connectors J16 through J9)
4311 B through 4318 B (connectors J32 through J25)
6.1.2.1.5 Extension Frame EF-03
Extension shelf 51
5101 A through 5108 A (connectors J24 through J17)
5101 B through 5108 B (connectors J40 through J33)
5111 A through 5118 A (connectors J16 through J9)
5111 B through 5118 B (connectors J32 through J25)
Extension shelf 52
5201 A through 5208 A (connectors J24 through J17)
5201 B through 5208 B (connectors J40 through J33)
5211 A through 5218 A (connectors J16 through J9)
5211 B through 5218 B (connectors J32 through J25)
Extension shelf 53
5301 A through 5308 A (connectors J24 through J17)
5301 B through 5308 B (connectors J40 through J33)
5311 A through 5318 A (connectors J16 through J9)
5311 B through 5318 B (connectors J32 through J25)
6.1.2.2 Recommended Tools
Oracle tools should be labeled “Property of ORACLE” with either a press-on Field Tool Identification label or Field Tool Identification wrap.
-
Safety glasses
-
Tie-wrap tool
-
Diagonal cutters
-
Flush cutters
-
Slotted screwdriver, 1/8-inch blade with 8-inch shank
-
3/8-inch shrink-wrap
-
Heat-shrink gun (hot air blower)
-
Torque screwdriver
-
Wire-wrap gun
-
22-gauge wire-wrap bit
-
24-gauge wire-wrap bit
Interface Cable Installation
Examine the labels on the ends of the interface cables to determine the system backplane connection location “FROM” information on label and DSX cross-connect panel location “TO” information on label for each cable.
Run the cables on the cable rack to the cross-connect panel on the Miscellaneous Frame in groups of eight. There are four groups per extension shelf and groups per control shelf (a total of 20 per control shelf). The jack numbering on the cross-connect panel determines which side of the frame to run the cable. Viewing the frame from the rear, cables going to jacks #1 through #32 are run on the right side of the frame and cables #33 through #64 are run on the left side of the frame.
Procedure — Install Interface Cable
-
Secure connector to its respective receptacle on the backplanes. See Interface Cable Installation.
-
Tie cables to the shelf cable tie bar at the rear of the shelf.
-
Pull slack from each cable towards the cross-connect panel.
-
Dress cable bundles neatly and tie to the cable tie bars at the side of the frame.
-
Lace the bundles to the cable rack.
Note:
All cables must be laced onto the top traverse arms of each frame. Only lacing is used from the top traverse arms and above, on the frame and on the cable rack.Note:
Where the cable leaves the cable rack, the cable must be protected with fiber paper through out the system.
Procedure — Preparing Cables for Wire-Wrap
6.1.3 LAN Ethernet Cable Installation for ACM
This section contains the procedures for installing the Local Area Network (LAN) Ethernet cable, see Figure 6-7 for the location of equipment. The LAN provides selected data to a remote host system through an Ethernet network. In the system, communications with the host is interfaced through an Application Communication Module (ACM). Communications with the ACM is accomplished through:
6.1.3.1 Customer Supplied Ethernet Cable Requirements
If a customer chooses to supply their own Ethernet cables for EAGLE (customer-supplied cables are not subject to Oracle warranty), the following requirements must be met:
Customer-supplied Ethernet cables for EAGLE must be shielded, meet the industry standard, and avoid dissimilar metals at the RJ45 connector interface. The required standards include:
Metallization (30 or 50µ in. Au over 50µ in. Ni), at the connector interface. The wire required follows: Category 5E SCTP 26AWG 7/34 tinned copper 4 PR per IEC 11801, TIA/EIA 568B, EN 50173 with Overall shield, 26 AWG stranded T.C. drain wire, UL CMR, C(UL) CMR rating, or other agency listing.
Signaling Cables (for example, T1, ATM) are EAGLE proprietary and must be purchased from Oracle.
6.1.3.2 Recommended Tools
Oracle tools should be labeled “Property of ORACLE” with either a press-on Field Tool Identification label or Field Tool Identification wrap.
-
Safety glasses
-
Diagonal cutters
-
Coax crimping tool
-
Tie-wrap tool
-
Flush cutters
-
Slotted screwdriver with 1/8-inch blade with 8-inch shank
-
Multimeter
LAN Ethernet Cable Installation
6.2 E5-ENET/E5-ENET-B and Fan Option, EDCM, E5-SM4G/E5-SM8G-B Cabling
E5-ENET/E5-ENET-B and EDCM Modules
The following cabling procedures apply to E5-ENET/E5-ENET-B,EDCM and E5-SM4G/E5-SM8G-B cards in the latest EAGLE.
6.3 User Upgrade Procedures
This section describes procedures for upgrading your ASM and TDM cards, and your DSM cards loaded with the MCPM application.
Note:
DSM and EDSM cards loaded with the MCPM application and the E5-MCPM-B card will be referred to as “MCPM cards.”6.3.1 Upgrading to E5-MCPM-B Module (MCPM)
Note:
Do not attempt this procedure during the first hour of the day (0000 to 0059).Note:
Throughout this document, the term MCPM refers to both the E5-MCPM-B (P/N 870-3089-xx) and the EDSM-2G loaded with the MCPM application (P/N 870-2372-03) cards unless specifically noted otherwise.The Primary MCPM card performs all measurements collection and reporting functions and provides on-card RAM storage for collected data and scheduled reports. The Secondary MCPM provides a redundant backup for the Primary module, and assumes collection and reporting responsibilities on the loss of the Primary. TCP/IP connections are used to deliver measurement reports from the Primary MCPM card to the customer via an FTP client. The FTP configuration can be customized to support automatic transfer of scheduled reports from the client to the server.
6.3.2 Measurement Collection and Polling Module (MCPM)
This procedure upgrades DSM cards loaded with the MCPM application (870-2371-03) to EDSM cards with 32 MBFSRAM and 2 GBRAM loaded with the MCPM application (870-2372-03).
Note:
DSM and EDSM cards loaded with the MCPM application will be referred to as “MCPM cards.”The Primary MCPM card performs all measurements collection and reporting functions and provides on-card RAM storage for collected data and scheduled reports. The Secondary MCPM provides a redundant backup for the Primary module, and assumes collection and reporting responsibilities on the loss of the Primary. TCP/IP connections are used to deliver measurement reports from the Primary MCPM card to the customer via an FTP client. The FTP configuration can be customized to support automatic transfer of scheduled reports from the client to the server.
6.3.3 Removing a Card in an Existing EAGLE System
Use this procedure anytime a card is removed from a previously operational EAGLE system for upgrade purposes. See Maintenance Guide for card replacement. Failure to use this procedure may result in equipment damage. Use the procedures at the beginning of this section before physically removing any cards.
attention:
Before performing any maintenance procedures on the EAGLE, make sure you wear a wrist strap connected to the wrist strap grounding point of the EAGLE System.Before removing, reseating, or initializing a card, inhibit any OAP terminal ports that are in-service normal (IS-NR) to ensure the card loads properly. No database updates or single command line entries should be made while the card is loading.
attention:
This procedure may interrupt service. When possible, perform maintenance during low traffic and database provisioning periods, such as the maintenance window.6.4 Fan Assembly Installation and Cabling
warning:
Do not carry exposed metal keys or tools in pockets or on belts when working on or around system equipment.warning:
Do not wear metal rings, watches, or jewelry on wrists or hands when working on system equipment or other related electrostatic sensitive components. Always wear a wrist strap or other electrostatic protection when handling printed circuit cards and other electrostatic sensitive devices.Caution:
Be sure to install the fan assembly 890-0001-04 before installing the HCMIM card.This section shows how to install the optional Fan Assembly 890-0001-04 and Fan Assembly 890-1038-01/890-1038-02. All of these fan assemblies can be installed in the standard frame and the Heavy Duty Frame. Be sure to determine which type of frame you have before performing these procedures.
6.4.1 Installing Fan Assembly 890-0001-04
Note:
Beginning with EAGLE software release 33.0, all systems with HCMIM cards must have the 890-0001-04 fan assembly installed.Tools needed:
-
#1 Flat screwdriver
-
#2 Philips screwdriver (long)
-
Fiber Paper (Approximately 2’ x 3’)
-
5/16” ratchet socket wrench
-
Tie Wraps
Procedure — Install and Retrofitting Fans
-
Determine which shelves will have HCMIM modules installed and be aware of hardware that needs to be retained or installed in a specific way.
-
Place a piece of fiber paper on the top of the shelf below where the fan is to be installed to ensure that nothing will drop into equipment below the new fan.
-
Make sure to pull both dummy fuses from the appropriate fuse locations for the A and B fan power. Use the following guidelines to determine fuse locations:
-
The fuse card located on the Fuse and Alarm Panel is marked FAN A and FAN B. Fuse positions 6, 12, and 18 are the correct locations on the FAP faceplate.
-
Fuse position 6 is for the fan unit directly below the x100 shelf.
-
Fuse position 12 is for the fan directly below the x200 shelf.
-
Fuse position 18 is for the fan directly below the x300 shelf.
-
All fans are to be fused at 3As, with blue flags, per feed. Fill out the fuse card completely.
-
Ensure the FAP fuse location for the fan is properly labeled.
-
-
If you are installing the fan assembly into an existing frame, remove the four screws (two on each side) that attach the air baffle to the mounting brackets. Do not remove the screws holding the side brackets to the frame at this time. Support the baffle while you remove the screws.
Figure 6-13 System Air Baffle
-
Remove the baffle through the front of the frame. Then, remove the two screws holding the left and right side baffle brackets to the frame and remove the brackets.
-
Install the new side brackets for the new fan tray into the frame. The side brackets are installed from the front of the frame just below the shelf containing that cards that require the fan. Use the 12-24-x1/2 screws provided to attach the brackets to the left and right front frame rails. The top screw hole is 5/16 inch below the shelf containing the cards. Be sure not to completely tighten the brackets at this time.
Figure 6-14 Attach side fan bracket to front frame rail
-
Slide the brackets in toward the center of the frame so the outside of the bracket is flush with the side of the frame as shown in Figure 6-15.
Figure 6-15 Slide the side fan brackets flush with the Frame
-
Verify whether the frame type is a standard or heavy duty so that you can ensure the fan tray bracket will be mounted correctly. Use the following mounting positions:
-
Use the side holes on the fan tray bracket that are closest to the front of the frame if you are installing in a standard frame.
-
Use the holes closest to the rear of the frame if installing in a heavy duty frame.
Figure 6-16 Side bracket mounting positions on fan tray bracket.
-
-
Insert the fan tray bracket (P/N 652-0012-01) into the space left by the baffle under the card shelf. The untightened side brackets will slide outward slightly to accommodate the fan tray bracket as it is inserted. They should remain flush against the fan tray bracket.
Figure 6-17 Insert fan tray bracket
Note:
When inserting the fan tray bracket, be sure not to pinch cables between the bottom of the shelf and the fan tray bracket. -
From inside the frame, screw the fan tray bracket to the side brackets with one hand while using the other hand to support the fan tray bracket. Use two 8-32 phillips screws for each side bracket. See Figure 6-18.
Figure 6-18 Attaching the fan tray bracket to the side brackets - inside front
-
Remove the new fan tray from the container. The fan tray is shipped with the three fans already installed.
Figure 6-19 Fan Tray
-
Insert the fan tray into the fan tray bracket. You might need to tilt the fan tray up as it is pushed in so that it is completely inserted into the bracket. After insertion, be sure the front of the fan tray is recessed in 1/2 inch with respect to the front frame rails.
Figure 6-20 Fan tray inserted into fan tray bracket in the frame- front view
-
When the fan tray is aligned and in place, attach the fan tray to the fan tray bracket by tightening the screws on the left and right sides of the rear of the fan tray bracket. There are two screws on each side. These screws must be tightened from the rear of the frame.
Figure 6-21 Tighten rear fan tray screws
-
At this time check and tighten all screws, including the screws holding the side brackets to the frame. The side bracket screws should be tightened fully from the rear of the frame. Use a long hex driver or flat head screw driver.
Figure 6-22 Tighten fan side bracket screws
-
Remove the piece of fiber paper on the top of the shelf below where the fan assembly was installed. This procedure is complete.
Caution:
Before powering up the fans, ensure that the shelf directly above the fan does not contain any empty slots. Install an air management card in any empty slots to ensure proper air flow. These filler cards have no electrical connection to the system. See Card Installation and Replacement for general card installation guidelines.
6.4.2 Installing Fan Cables
On the control and extension shelf backplanes, the connectors are marked A FAN POWER and B FAN POWER.
-
Control shelf:
On backplane (P/N 850-0330-06 or -07) the connectors are A FAN POWER, J-9 and B FAN POWER, J-8.
These connectors are located at the upper middle of the backplane on both the control shelf and the extension shelves.
-
Extension shelf: The backplane connectors are A, J-3 and B J-2.
-
For A fan power:
The fan cable 830-1157-01 is included with the fan assembly. Plug one end of the cable into J-9 on the backplane. Route the cable to the left of the frame, faced from the rear, and to the assembly, to the connection marked FAN A POWER.
-
For B fan power:
Plug one end of the cable 830-1157-01 into J-8 on the backplane. Route the cable to the right of the frame, faced from the rear, and to the fan assembly, to the connection marked FAN B POWER. Form and dress the two cables together and check the security of all of the connections.
6.4.3 Powering Up the Fan Assembly
All fans are fused at 3A (blue) per feed.
warning:
Before powering up the fans, ensure that the shelf above the fan does not contain any empty slots. Install the air management card in any empty slots. See Card Installation and Replacement for general card installation guidelines.Procedure — Power up Fan Assembly
6.4.4 Installing Fan Assembly 890-1038-01 or 890-1038-02
Tools needed:
-
#1 Flat screwdriver
-
#2 Philips screwdriver (long)
-
Fiber Paper (Approximately 2’ x 3’)
-
Tie Wraps
6.4.5 Installing Fan Cables
On the control and extension shelf backplanes, the connectors are marked A FAN POWER and B FAN POWER.
-
Control shelf:
On backplane (P/N 850-0330-06 or -07) the connectors are A FAN POWER, J-9 and B FAN POWER, J-8.
These connectors are located at the upper middle of the backplane on both the control shelf and the extension shelves.
-
Extension shelf: The backplane connectors are A, J-3 and B J-2.
-
For A fan power:
The fan cable is included with the fan assembly. Plug one end of the cable into J-9 on the backplane. Route the cable to the left of the frame, faced from the rear, and to the assembly, to the connection marked FAN A POWER.
-
For B fan power:
Plug one end of the cable into J-8 on the backplane. Route the cable to the right of the frame, faced from the rear, and to the fan assembly, to the connection marked FAN B POWER. Form and dress the two cables together and check the security of all of the connections.
6.5 Source Timing
The EAGLE connects to the customer provided Building Integrated Time System (BITS) clocks through the backplane of the control shelf. The BITS clock provides a primary and secondary set of two separate clock signals; a composite (64KHz) clock signal and a high speed (2.048Mhz or 1.544Mhz) clock signal.
The section provides information about the High‑Speed Source Timing feature and instructions on how to implement the feature. Procedures include the replacement of the composite clock cables.
Note:
This feature does not cover the replacement of the control shelf, the control shelf backplane, or an EAGLE software upgrade. For these items, contact My Oracle Support (MOS) for assistance.Source Timing Overview
The High‑Speed (HS) Source Timing feature offers a mode of operation that allows a high speed capable (T1 or E1 rate) Link Interface Module (LIM‑ATM) or E1/T1MIM installed in an EAGLE STP to receive its transit timing reference directly from an external HS Source clock source, instead of slaving to the timing information contained in the received data. The timing information is then encoded into the T1 or E1 transmitted data stream used to synchronize downstream equipment. The site clock sources (both HS and composite) are connected with an RS422 compatible cable to the primary and secondary clock inputs of the EAGLE STP.
The high‑speed Source clock source provides the EAGLE STP with a second system clock input in addition to the original composite clock. Timing signals from both system clocks is distributed within the EAGLE STP to all LIM card slots.
The HS Source Timing feature is integrated into the EAGLE Control Card set.
Implementation of the HS Source Timing feature might require the correct Control Card set, the installation or presence of at least one ATMLIM card or E1/T1MIM, the replacement of both composite clock cables or adding new cables, and the provisioning of at least one ATMLIM card or E1/T1MIM. ATMLIM cards or E1/T1MIM that do not use the high‑speed clock source and LIM cards that continue using the composite clock source do not require any changes to card provisioning.
OAP terminals must be inhibited before replacing the Control Card set for the HS Source Timing feature to ensure that no OAP updates are inadvertently sent to the database during the implementation.
The composite clock cables connect the site’s composite (BITS) clocks with the EAGLE STP control shelf. Implementation of the HS Source Timing feature requires the replacement of both composite clock cables with two new HS Source clock cables (RS422 compatible) on control shelf backplane (P/N 850‑0330‑06 or ‑07 and later).
Only ATMLIM cards or E1/T1MIM can be configured or re‑configured for the HS Source Timing feature. Once the baseline hardware requirements for the HS Source Timing feature have been met, see the Source Timing Feature Requirement Matrix, install the cards.
Caution:
These are redundant systems to allow service during normal maintenance. When repairs require a total power disconnect, both input supply sources must be disconnected. This will cause service interruption and takes down the systems.-
Install an ATM card, add the card to the system database, and enable it for the HS Source Timing feature (ent‑slk:atmtsel=external); or
-
Install an E1/T1MIM, add the card to the system database, and enable it for the HS Source Timing feature (ent‑e1:e1tsel=external).
Reconfigure any existing ATMLIM card or E1/T1MIM to use the HS Source Timing feature. LIM cards that will continue using the composite clock will not require any changes to the card provisioning.
Note:
The EAGLE terminal output screens refer to the composite clocks as Building Integrated Timing Source (BITS) clocks. In this document, references to BITS and composite clocks are interchangeable.Source Timing Site Requirements
Implementation of the HS Source Timing feature requires the following software and hardware baselines:
- One of the following Control Card/Software Release sets:
- E5-based Control Cards with Software Release 40.1 or later
Note:
See "Hardware Baseline Table" in Release Notes for compatible card and control shelf and extension backplane part numbers. - Control shelves with backplane (P/N 850‑0330‑03 or 04), if adapter cables
P/N 830‑1183‑01 are installed with HS
clock cables P/N 830‑0873‑xx or P/N 830‑1189‑xx.
Note:
Replace the existing composite clock cables (P/N 830‑0226‑xx) with RS422 compatible HS Source and composite clock cables P/N 830‑0873‑xx or P/N 830‑1189‑xx. For control shelves with backplane (P/N 850‑0330‑06 or ‑07 or later), connect the cables to J48 and J49 (primary and secondary BITS) and connect the other ends to the site clock sources.Note:
For control shelves with backplane (P/N 850‑0330‑03 or 04), connect the adapter cables (P/N 830‑1183‑01) between connectors J57 and J56 (ACLK3 and ACLK4) on the backplane and to the site HS clock source using HS clock cables. Leave the existing composite clock cables connected to J42 and J41 (Primary and Secondary BITS). - Control shelves with backplane P/N 850‑0330‑06 or ‑07 or later using HS Source and composite clock cables
P/N 830‑0873‑xx or P/N 830‑1189‑xx.
Note:
Replace the existing composite clock cables (P/N 830‑0226‑xx) with RS422 compatible HS Source and composite clock cables P/N 830‑0873‑xx or P/N 830‑1189‑xx. For control shelves with backplane (P/N 850‑0330‑06 or ‑07 or later), connect the cables to J48 and J49 (primary and secondary BITS) and connect the other ends to the site clock sources. - ATMLIM card(s) or E1/T1MIM(s)
- High‑speed clock source (T1 or E1)
Source Timing Feature Requirement Matrix
Use Table 6-2 to identify the hardware or software that is required to prepare your EAGLE STP for the HS Source Timing feature. Perform the procedures in the order listed. Skip any procedure that does not apply.
Note:
Perform the procedures mentioned in this document during a maintenance window.Table 6-2 Feature Requirement Matrix
If you do not have... | do this... | using procedures... | Notes |
---|---|---|---|
Control shelf backplane P/N 850‑0330‑06 or ‑07 or later |
Replace the backplane |
Contact My Oracle Support (MOS) for assistance. |
|
If you have a control shelf with backplane P/N 850‑0330‑03 /04, install adapter cable (P/N 830‑1183‑01) and HS clock cable (P/N 830‑0873‑xx) |
See HS Source and Composite Clock Cables on Backplane P/N 850‑0330‑03/04. |
||
HS Source and composite clock cables (P/N 830‑0873‑xx) installed |
Replace composite clock cables with HS Source and composite clock cables and adapter cable if necessary |
See HS Source and Composite Clock Cables on Backplane P/N 850‑0330‑06/07 or A Clock and B Clock Cable Replacement. |
Replace one cable at a time. |
In an EAGLE using legacy Control Cards: GPSM ll cards (P/N 870‑2360‑01) TDM (P/N 870‑0774‑10 or later). Note: Beginning with EAGLE Software Release 31.6 TDM cards must be P/N 870‑0774‑18 to support Global Timing Interface (TDM‑GTI). |
Contact My Oracle Support (MOS) for assistance replacing the MASP. |
Always start with standby MASP |
|
In an EAGLE using E5-based Control Cards: E5-MASP cards |
Contact My Oracle Support (MOS) for assistance replacing the MASP. |
Always start with standby MASP |
|
E1/T1MIM installed |
Install E1/T1 |
Refer to Maintenance Guide or Database Administration - SS7 User's Guide. |
|
E1/T1MIM configured |
Configure E1/T1 |
Adding an SS7 Signaling Link or Provisioning the E1/T1 in the Database as described in Database Administration - SS7 User's Guide. |
Tools and Equipment
- Two high speed Source and composite clock cables (P/N 830‑0873‑xx)
- Two adapter cables (P/N 830‑0846‑01) if using control shelf backplane (P/N 850‑0330‑03/04) with HS cables (P/N 830‑0873‑xx).
- T1 or E1 LIM card(s)
- ESD safe slotted screw driver
- Cable ties
6.5.1 HS Source and Composite Clock Cables on Backplane P/N 850‑0330‑06/07
On systems with backplane (P/N 850‑0330‑06/07) the HS source and composite clock cable (P/N 830‑0873‑xx) is used to transmit the clock outputs from the customer HS source and composite clock sources to the EAGLE control shelf backplane, providing the EAGLE with a second synchronized system clock. The EAGLE connects to the site source clock through two DB 15 style connectors (J49 and J48) on the backplane of the control shelf for primary and secondary clock signals. The two connectors are labeled Primary BITS and Secondary BITS. Both primary and secondary clock signals are sent to each terminal disk module (TDM). The TDM cards select between the primary and secondary clock signals to provide A and B system clocks to the rest of the EAGLE.
This procedure replaces the existing composite clock cables (P/N 830‑0226‑xx) with RS422 compatible cables (P/N 830‑0873‑xx or P/N 830‑1189‑xx) connected to the customer HS and composite clock sources.
Caution:
A system with DS0A links cannot run without a composite clock source. Take extreme caution when replacing the composite clock source cables. Remove one cable at a time and confirm between removals that the other composite clock source is active.Caution:
Perform this procedure during a maintenance window.Caution:
Prior to adding or replacing the high‑speed source and composite clock cables, perform an EAGLE system health check.Caution:
HS clock alarms are only generated if an external BITS clock source is being used.Caution:
Always replace the IDLE clock cable first, whether it is the primary or secondary cable position. After the replacement of the first (IDLE) cable position, ensure the system reports the clock status properly with an ACTIVE and IDLE clock output. If the output reports the correct status the ACTIVE cable can be disconnected for replacement. Disconnecting the ACTIVE cable will transition the previously IDLE clock to the ACTIVE clock forcing the system to use the new clock cable that was installed.Note:
In this procedure, the high‑speed clock status indicated in the output of therept-stat-clk
command reflects the presence of at least one ATM LIM card or E1/T1 MIM in the system. The status fields remain empty until the card is configured to use the high‑speed clock.
Procedure — Replace or Add HS source Timing Clock Cables with backplane (P/N 850‑0330‑06/07)
6.5.2 HS Source and Composite Clock Cables on Backplane P/N 850‑0330‑03/04
On systems with control shelf backplane (P/N 850‑0330‑03/04), the high‑speed source clock cable (P/N 830‑0873‑xx or P/N 830‑1189‑xx) sends only high‑speed clock signals to the EAGLE. The existing composite clock cables (P/N 830‑0226‑xx) continue to provide the low‑speed clock connections to connectors J42 and J41 (Primary BITS and Secondary BITS) on the backplane. The HS cables (P/N 830‑0873‑xx or P/N 830‑1189‑xx) send the HS primary and secondary clock signals through adapter cables (P/N 830‑0846‑01) to connectors J57 and J56 on the backplane. The two connectors are labeled ACLK3 and ACLK4.
This procedure describes the steps required to install the HS clock cables on the EAGLE with control shelf backplane (P/N 850‑0330‑03/04) using adapter cable (P/N 830‑0846‑01).
Caution:
A system with DS0A links cannot run without a composite clock source. This procedure requires removing and replacing the ACLK3 cables to frame 3 (shelves 4100, 4200, 4300) and frame 4, ACLK4 (shelves 5100, 5200, 5300). Take extreme caution when removing and replacing the ACLK cables. Remove one cable at a time and confirm before removal that the BCLK clock source is active to that frame.Caution:
Perform this procedure during a maintenance window.Caution:
Prior to adding or replacing the high‑speed source and composite clock cables, perform an EAGLE system health check.Caution:
HS clock alarms are only generated for ATM LIM cards and E1/T1 MIM if the card is provisioned to use the HS clock.Caution:
Always replace the IDLE clock cable first, whether it's the primary or secondary cable position. After the replacement of the first (Idle) cable position, ensure the system reports the clock status properly with an active and idle clock output. If the output reports the correct status you are know able to replace the active cable which will force the system to use the new clock cable (idle) position and it will transition state to active.Caution:
Connectors ACLK3 and ACLK4 propagate system A clocks to frame 3 (shelves 4100, 4200, and 4300) and frame 4 (shelves 5100, 5200, 5300). System A clock signals to cards in these shelves will be lost during this procedure. If the EAGLE contains these shelves with cards installed the cards switch automatically to the system B clock sources when the A clock sources are removed.Note:
In this procedure, the high‑speed clock status indicated in the output of therept-stat-clk
command reflects the presence of at least one ATM LIM card or E1/T1 MIM in the system. The status fields remain empty until the card is configured to use the high‑speed clock.
Procedure — Replace or Add HS source Timing Clock Cables with:backplane (P/N 850‑0330‑03/04)
6.6 A Clock and B Clock Cable Replacement
Proper support for HMUX and alarm reporting require that all A and B clock cables be of P/N 830-0398-xx (domestic) or P/N 830-1150-xx (international). Clock cables of P/N 830-0404-xx must be replaced. The A and B clock cables typically are from the control shelf and those coming in from an extension shelf. These cables contain proper alarm alert capabilities and support HMUX. See Figure 6-37 and Figure 6-38.
This procedure can also be used for regular clock cable replacement.
Perform the replacement during a maintenance window and prior to fan assembly installation.
Figure 6-37 Cable (P/N 830-0404-xx)
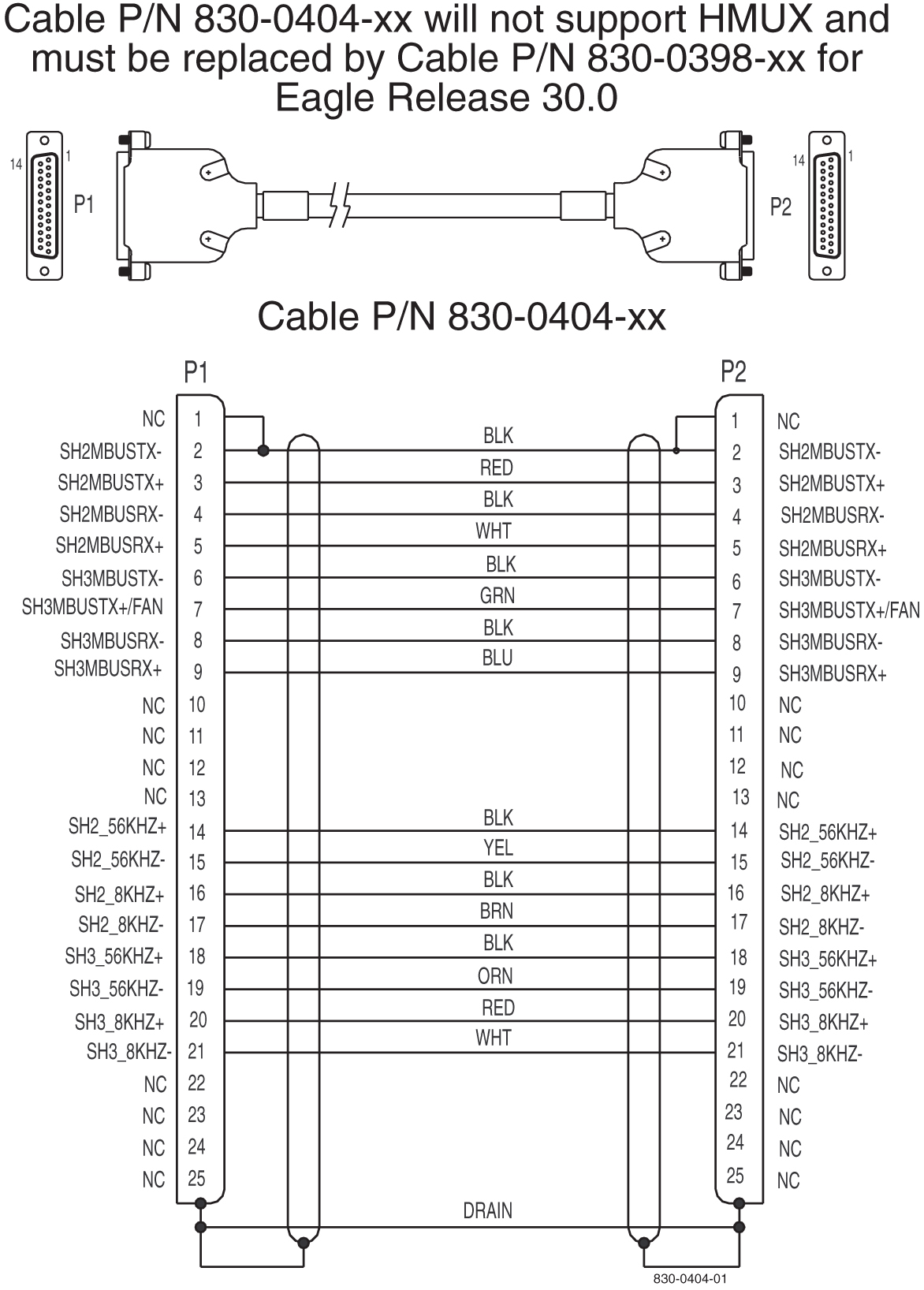
Figure 6-38 Cable 830-0398-xx or 830-1150-xx
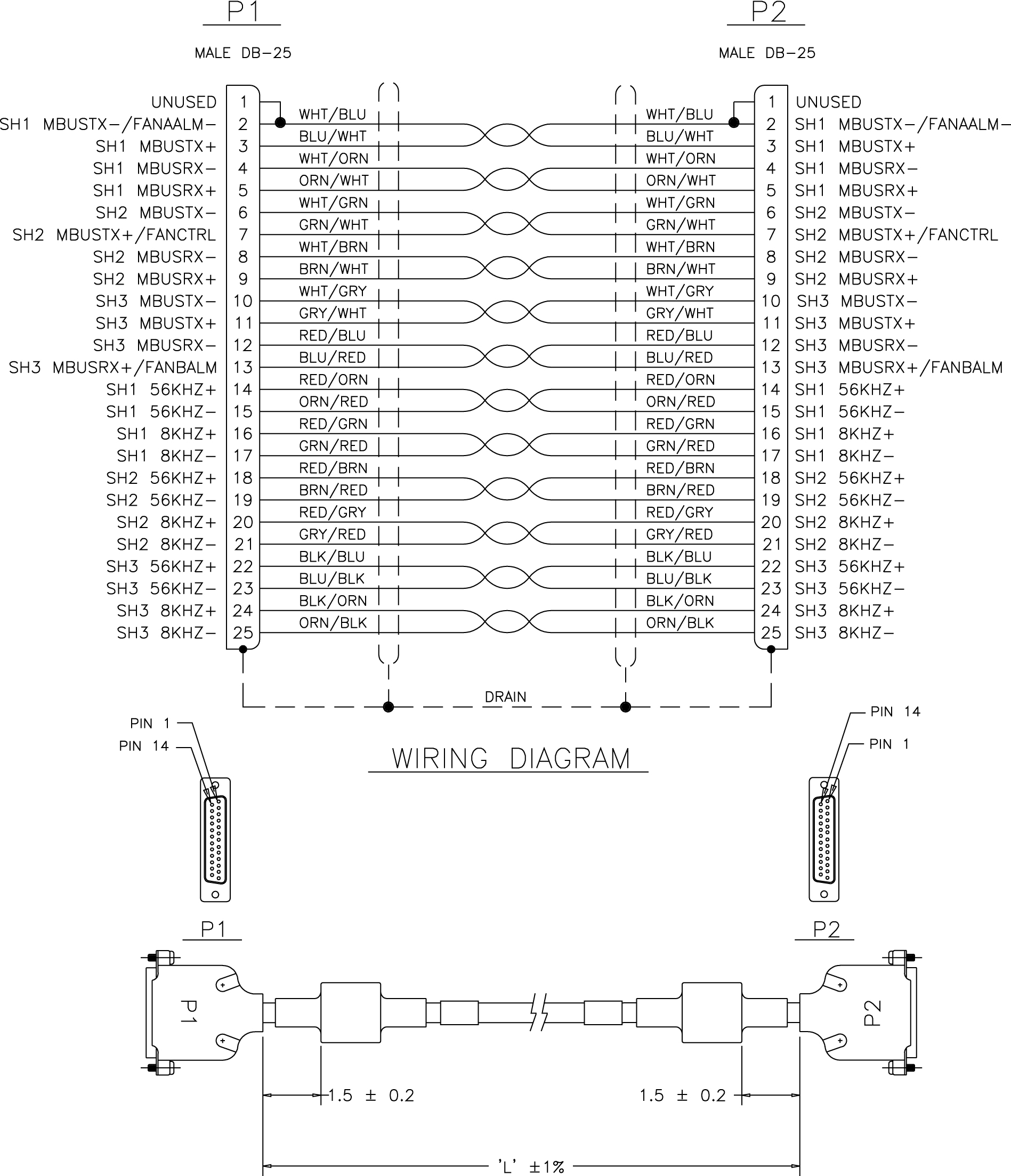
6.7 Termination of Alarm, Clock Supply, and Terminal Cables
Termination information for the alarm, Building Integrated Timing System (BITS), and terminal cables is furnished in the “Cable Running List” in the Equipment Specification for the site.
All of the alarm and clock supply cables are shielded and contain wires with solid conductors. They are intended for wire-wrap terminations at the customer end. The terminal cables have connectors on both ends.
danger:
Always wear a wrist strap or other electrostatic protection when handling printed circuit cards and other electrostatic-sensitive devices.Recommended Tools
Oracle tools should be labeled “Property of ORACLE” with either a press-on Field Tool Identification label or Field Tool Identification wrap.
-
Safety glasses
-
Tie-wrap tool
-
Diagonal cutters
-
Flush cutters
-
Wire-wrap gun and bit
-
Slotted screwdriver with 1/8-inch blade and 8-inch shank
-
Stripper
-
Heat gun
6.7.1 Alarm Cable Termination
The rack alarm cable for the control frame may be factory installed at both ends or the row alarm cable may come from the factory installed at the alarm end-panel only.
danger:
Always wear a wrist strap or other electrostatic protection when handling printed circuit cards and other electrostatic-sensitive devices.warning:
Always trim tie-wraps flush and turn the trimmed tie-wraps to the rear of the cable bundle, when facing the back of the frame.The backplane alarm ports are:
-
FAP (Frame and Alarm Panel) in the control frame J13 on 850-0330-06 or -07
-
FAP extension frame 00 J15 on P/N 850-0330-06 or -07
-
FAP extension frame 01 J32 on P/N 850-0330-06 or -07
-
FAP extension frame 02 J46 on P/N 850-0330-06 or -07
-
FAP extension frame 03 J61 on P/N 850-0330-06 or -07
-
FAP extension frame 04 J68 on P/N 850-0330-06 or -07
-
End panel J34 on P/N 850-0330-06 or -07 (use cable row alarm cable 830-1145-01)
-
J35 and J66 o 850-0330-06 or -07 to holdover clock
-
J69 on 850-0330-06 or -07 to OAPF
-
LMC J47 on850-0330-06 or -07
-
RMC J33 on 850-0330-06 or -07
From the rear of the frame these cables should be routed from the connector around the left side of the frame. Route the cables up the side of the frame to the FAP and secure the cables with lacing cord to the cross arms on the side of the frame. Across the top of the frame secure the cables to the cross arms above the FAP with lacing cord also.
Note:
Alarm cables should not be formed with power cables and should have a lacing cord approximately every three inches. There should be no less than two lacing cord ties between frames.Note:
If the end panel does not mount on the control frame, the cable will route the same as alarm rack cables, from port J34 on backplane 850-0330-06 or -07 from the rear of the frame, up the left side of the frame, across the top of the FAP, and formed and dressed with the alarm rack cables to the end panel.The following cables have connectors for termination on the control shelf. The cables listed below are cross-referenced for additional connector information:
-
Remote Maintenance Center Alarm Connector and unresolvable-reference.html#GUID-7AE0A7A2-DE22-4A15-A307-9BF3EA4A0C09 (RMC)
-
Local Maintenance Center Alarm Connector and unresolvable-reference.html#GUID-E2D259B1-1A5E-4512-86DB-1C51CDDBD40F (LMC)
-
Rack Alarm Connectors (RALM0 - RALM5)
-
Row Alarm Connector and Row Alarm Cable (ROW ALARM)
-
External Alarm Cable (Custom) and External Alarm Connector (XALM)
Cables are supplied as follows:
-
With the exception of the rack alarms and the row alarm, one of each type of alarm cable is supplied for each system.
-
One rack alarm cable is supplied for each Control, Extension, or OAP Frame present in the system.
-
One row alarm cable for each system equipped with an alarm end panel containing alarm indicator lamps.
6.7.2 Terminate Clock Supply Cables
The Building Integrated Timing System (BITS) clocks come directly from the central office BITS clock source or indirectly from an optional holdover clock installed in the system.
See Holdover Clock Installation for optional holdover clock installation information.
Refer to BITS Clock Connectors for cable connector information.
6.7.3 Terminal Cables
There are 16 I/O ports on the control shelf backplane that are used to support external printers, terminals, or modems.
Use terminal/printer cable 830-0535-xx or 830-1154-xx. Different combinations of adapters are possible, see Table 6-3.
Refer to Cables and Adapters for detailed cable and adapter connector information.
6.8 Holdover Clock Installation
The holdover clock option and its associated output panel are normally factory installed in a miscellaneous frame. Use the following procedures to complete the holdover clock installation.
Card Placement
The holdover clock cards must be installed in the positions illustrated in Figure 6-43. Check that the proper cards are installed in the indicated locations.
Figure 6-43 Holdover clock
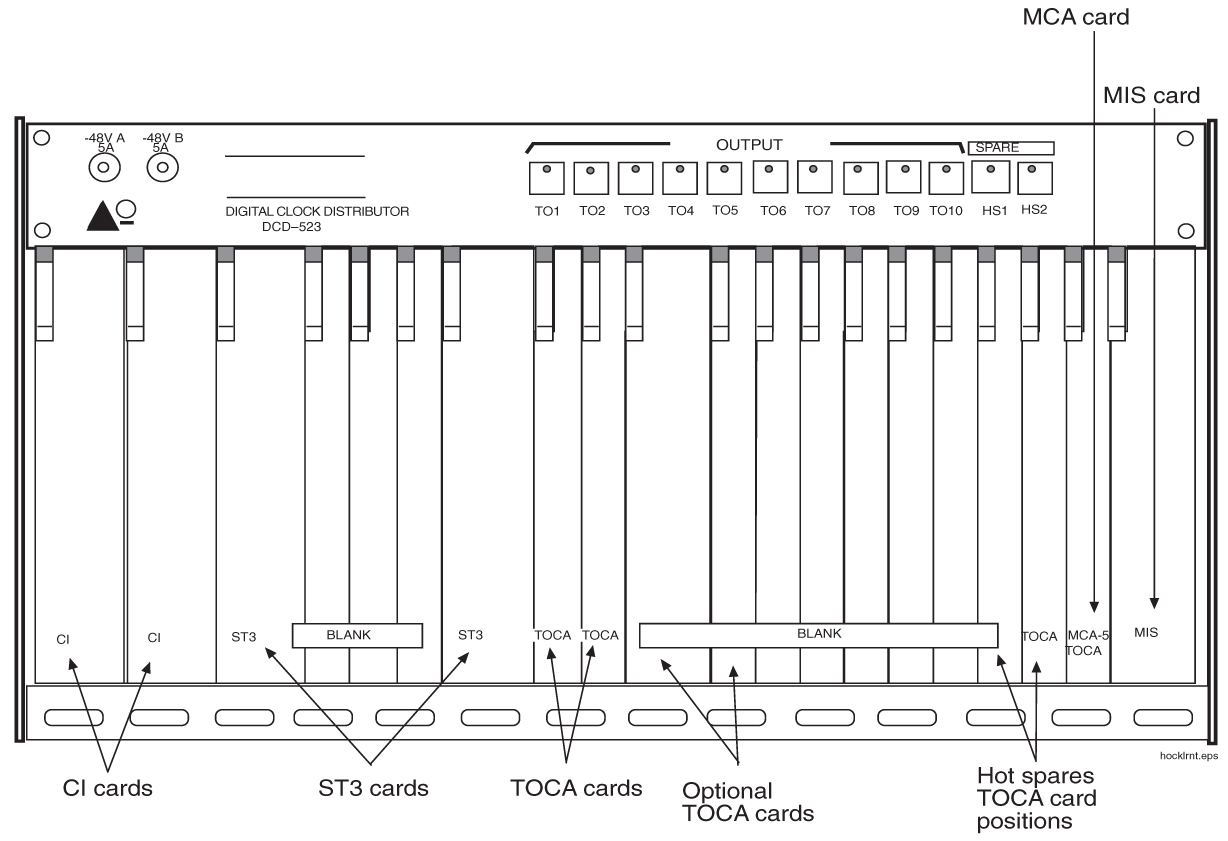
Recommended Tools
Oracle tools should be labeled “Property of ORACLE” with either a press-on Field Tool Identification label or Field Tool Identification wrap.
-
Safety glasses
-
Wire-wrap tool and bit
-
Diagonal cutters
-
Flush cutters
-
Slotted screwdriver with 1/8-inch blade and 8-inch shank, preferred.
-
Phillips screwdrivers, #2 and #3
-
3/8-inch shrink-wrap
-
Heat-shrink gun (hot air blower)
6.8.1 Output Panel Connections
The following output panel connections are factory installed and should be checked during installation.
TOCA Ribbon Cables
Timing Output Composite Clock Automatic (TOCA) ribbon cable; check to insure that the ribbon cables connecting the holdover clock with the output panel are connected as shown in Figure 6-46. OUT 1 on the holdover clock to J1 on the output panel and OUT 2 on the holdover clock to J2 on the output panel
Note:
These cables connect the clock outputs from the TOCA cards to the output panel.TOLA Card
When Using a Timing Output Logic Clock Automatic (TOLA) card; only terminate the clock cable leads to the odd pin positions 1, 3, 5, 7, and 9. Set DIP switch settings to the OFF position. Once switches are set, seat the card.
Figure 6-44 TOLA Source Timing Leads
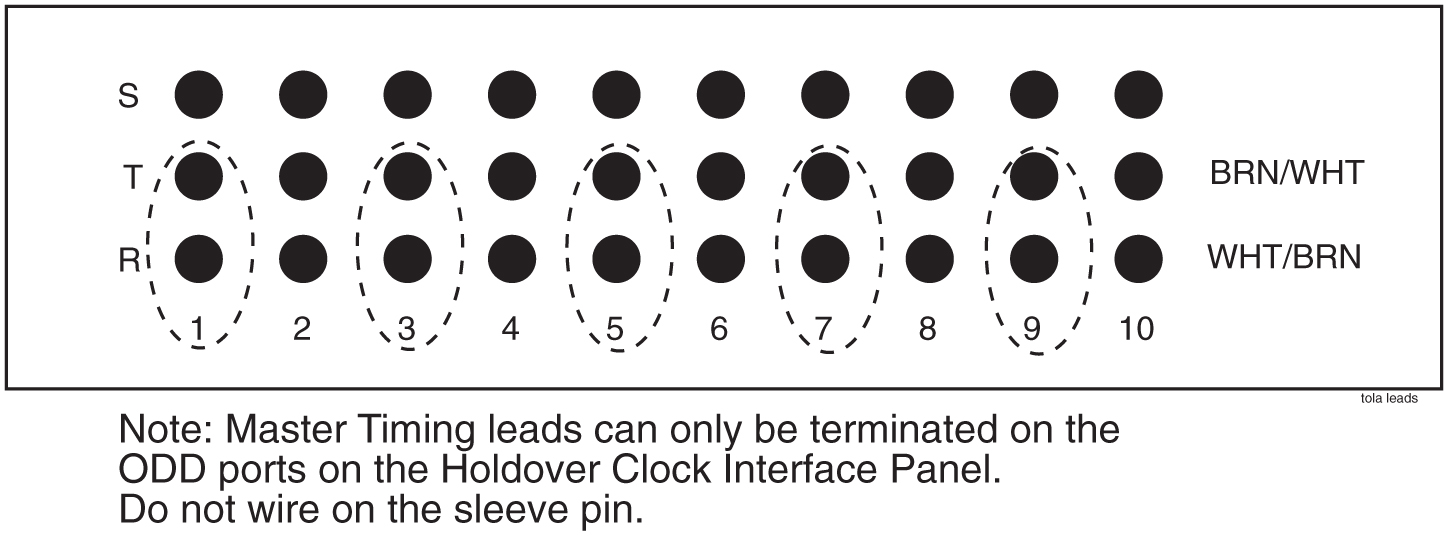
Output Panel Frame Ground
Check that the output panel frame ground cable is installed between TB2 on the output panel and an output panel mounting screw, see Figure 6-46.
Note:
This cable (P/N 690-0009) consists of black #16 AWG and a terminal ring.Power Connections
Check that the holdover clock power connections are installed according to Table 6-3 for holdover clock and fuse and alarm panel connections.
See Figure 6-45 and Figure 6-46 for holdover clock connector locations.
See Figure 6-47 and Figure 6-48 for fuse and alarm panel connector locations.
Table 6-3 Holdover Clock Wire Colors and Connections
Holdover Clock Connector | Wire Color | FAP Connection |
---|---|---|
TB1 –48VDC |
Red |
B side –48VDC #1 |
TB1 RTN |
Black |
B side –48VDC return #1 |
TB2 –48VDC |
Red |
A side –48VDC #1 |
TB2 RTN |
Black |
A side –48VDC return #1 |
TB1 GND |
White |
A side Chassis GND |
TB2 GND |
White |
B side Chassis GRD |
Figure 6-45 Holdover Clock Power Connector
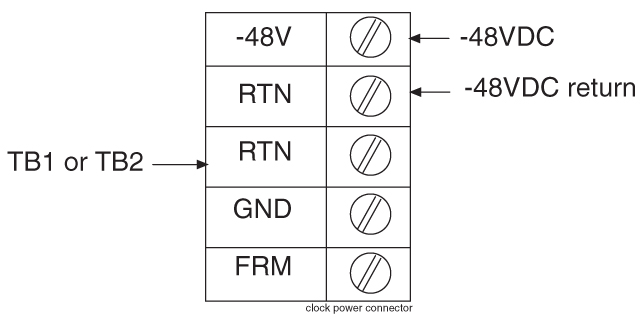
6.8.2 Holdover Clock Switch Settings
Set the switches on the back of the holdover clock to the following positions, see Clock Input DIP Switch Settings:
-
SHELF MODE (SW1) - ST3 (down)
-
POWER ALARM (SW2) - MAJ (down)
-
HOLDOVER ALARM (SW3) - MAJ (down)
-
REFA (SW4) - TERM (down)
-
REFB (SW5) - TERM (down)
6.8.3 Clock Input DIP Switch Settings
The Dual In-line Package (DIP) switch settings for the Clock Input are:
-
Transmission 1.544 mb -TI (On)
-
Extended Superframe Format - ESF (On)
-
Bipolar 8Bit Zero Substitution - B8ZS (On)
Figure 6-46 Holdover Clock and Output Panel, Rear
The Fuse and Alarm Panel connections for the Holdover Clock are shown in Figure 6-47.
Figure 6-47 Holdover Clock FAP Connections
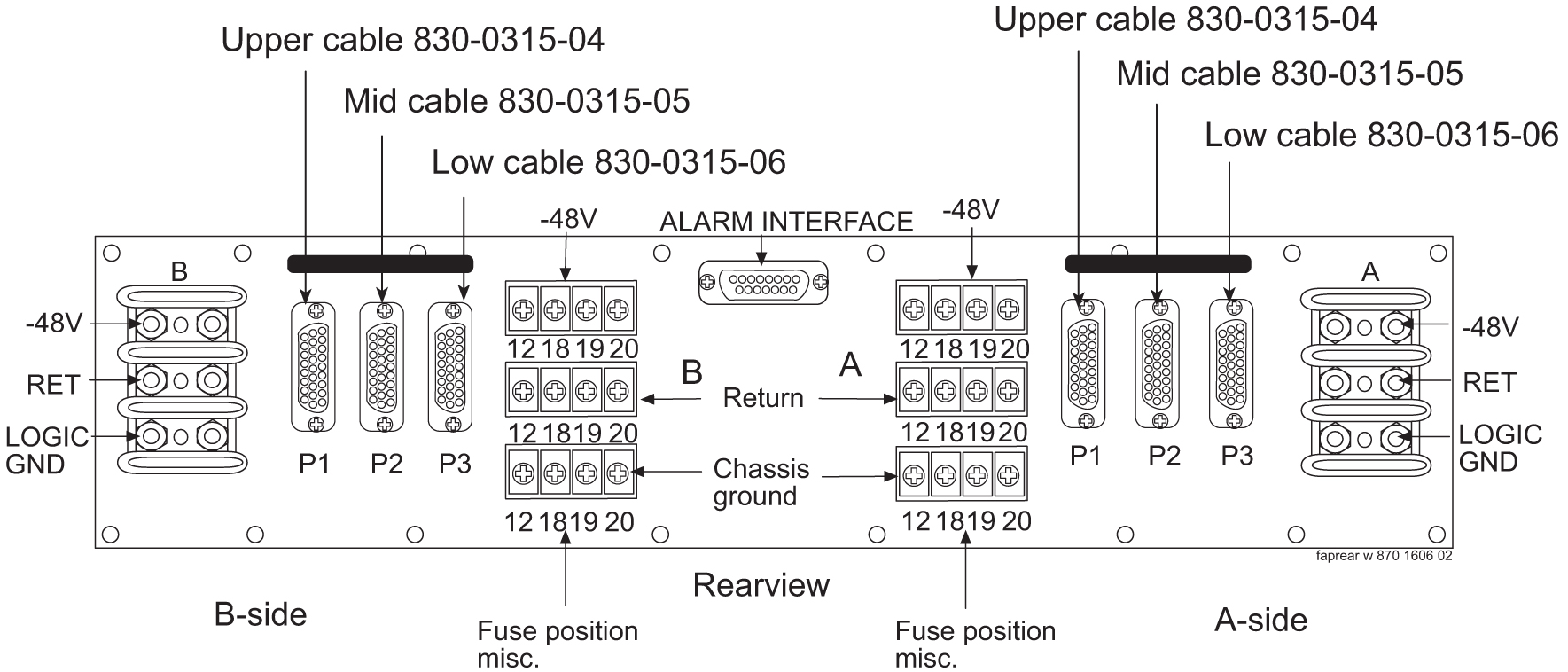
Figure 6-48 Holdover Clock FAP Connections
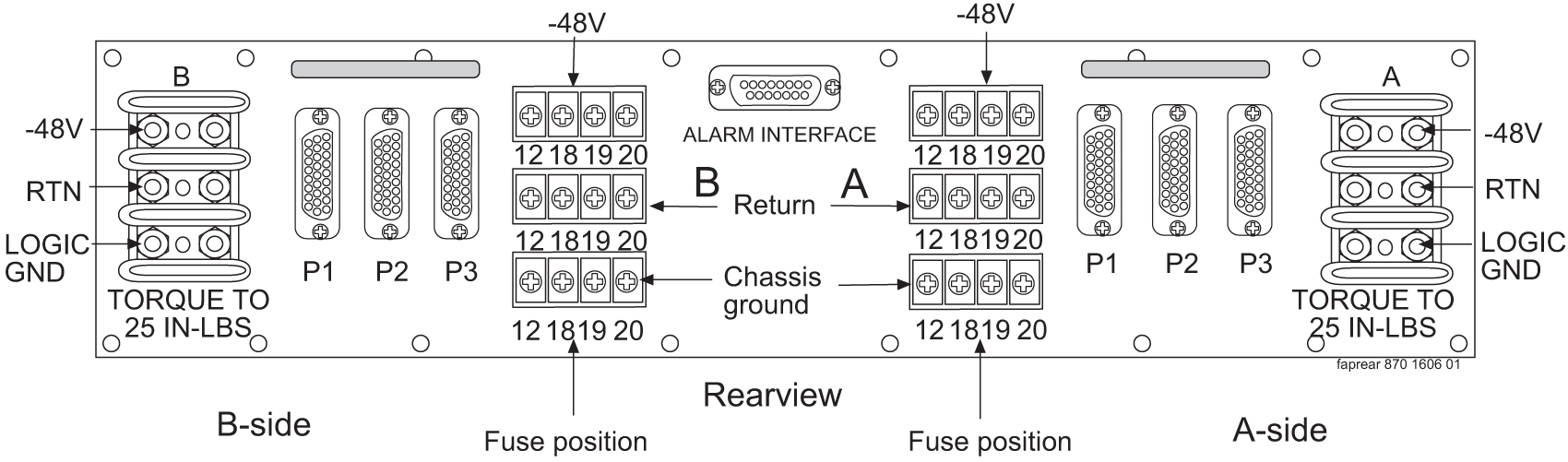
6.8.4 Output Panel Connections
The following output panel connections are made during installation.
Connections on the system backplane:
-
First Building Integrated Timing System (BITS) clock cable to Primary BITS connector on J42, and connector J49 on backplane (P/N 850-0330-06 or -07), J49.
-
Second BITS clock cable to the SECONDARY BITS connector J48 on backplane (P/N 850-0330-06 or -07).
6.8.5 Holdover Clock Alarm Connections
The installation connections are shown in the wiring layouts in Figure 6-50 and Figure 6-51.
A holdover clock alarm cable is used to send alarms from the holdover clock to the control shelf backplane.
6.9 Ohms Converter International Market
The ohms converter is used mostly outside of North America. The converter Super Multiple-Interface Cross-Connect (SuperMIX) is a modular device for cross-connecting, patching, and monitoring these digital signal rates:
-
E1 (2.048 Mb/s at 120 Ohms impedance)
The third party SuperMIX modules backplanes will be configured to accommodate a variety of input/output (I/O) termination connector types. Any combination or “mix” of backplanes in one chassis is acceptable. Refer to Telect® “SUPER MULTIPLE-INTERFACE CROSS-CONNECT (SUPERMIX) USER MANUAL” 110339 issue A Rev. 1
Note:
This information is for 120 to 75 ohms only.Figure 6-52 Miscellaneous Frame with 120 Ohm Converter
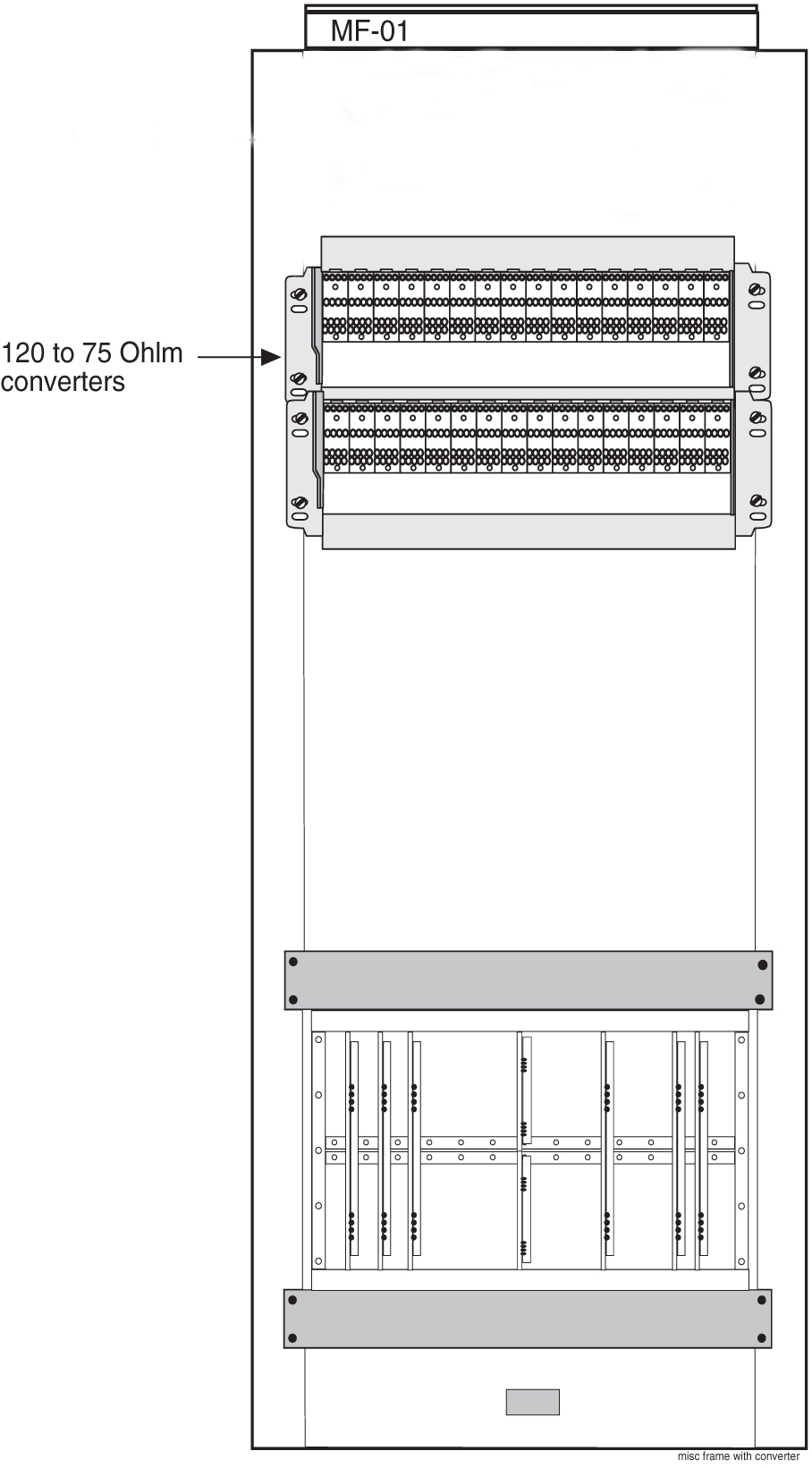
Note:
Customers may purchase the miscellaneous frame from Oracle.Table 6-4 Discontinued Legacy Part Numbers
Part Numbers | OEM part numbers | Description |
---|---|---|
804-0982-01 or 804-0982-R01 | 010-0000-2701 | Chassis |
804-0983-01 or 804-0983-R01 | 010-2704-1100 | Wire-wrap |
804-0984-01 or 804-0984-R01 | 010-2704-1200 | Bayonet Connector (BNC) |
Note:
There is no compatibility between the discontinued Legacy hardware and the replacement hardware; for reference only. No longer available for new deployment.Table 6-5 Telect® Replacement System for Cross-Connect Implementation
Manufacturer Part Number | Description | Description |
---|---|---|
DNX-2323 | 84-Term/21-Module, 23" x 5.25" Chassis | Chassis |
DNX-9324 | Wire-Wrap front to Wire-Wrap rear Module | Wire-wrap |
DNX-9321 | Wire-Wrap front to BNC rear | Bayonet Connector (BNC) |
Note:
Power distribution and replacement ohm converters are to be supplied by the customer.Figure 6-53 120 Ohms Converter and Shelf
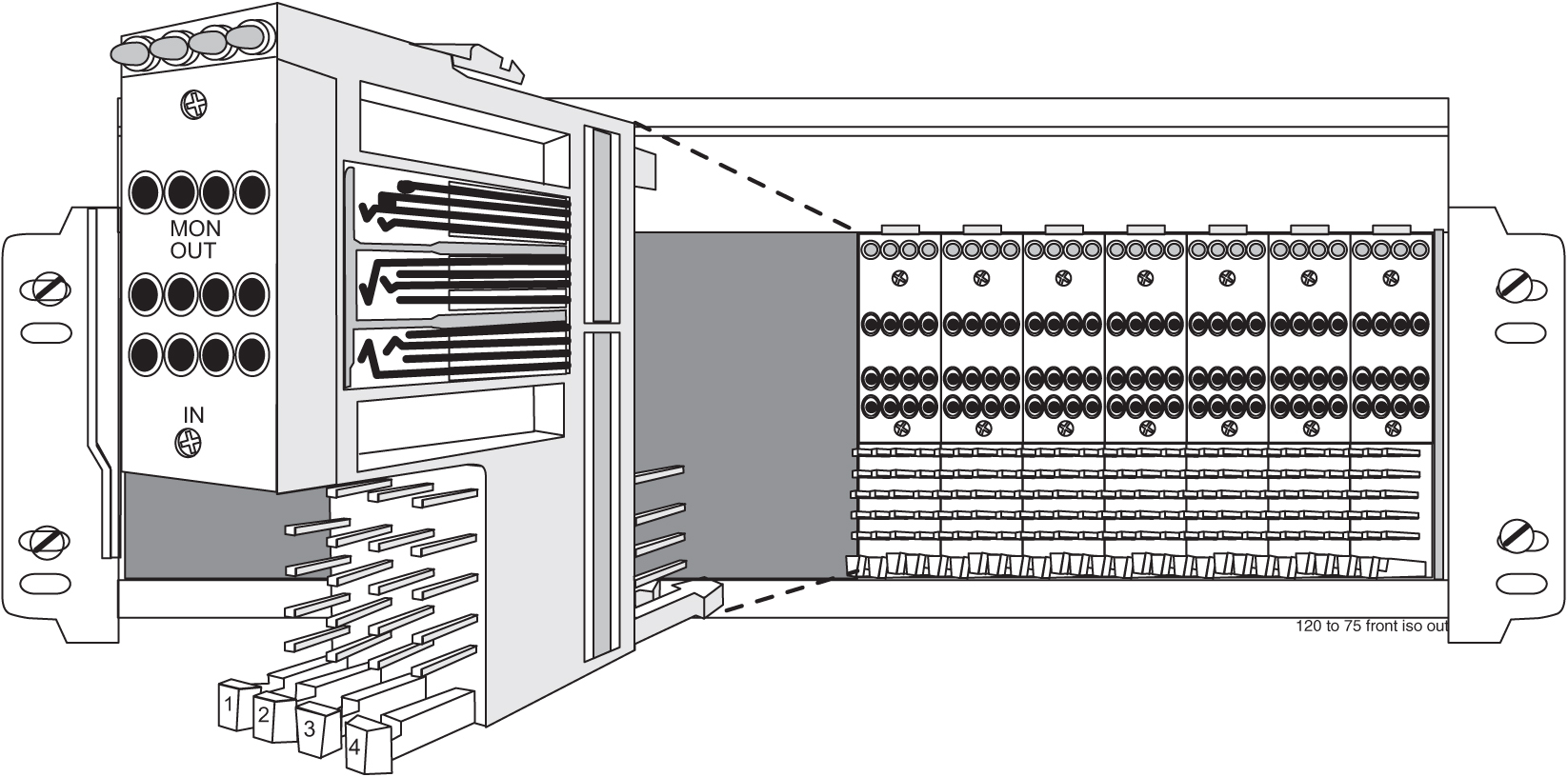
Table 6-6 Physical Conditions
Mechanical |
|
Insertion force |
4.17lb (1.9kg) average |
Withdrawal force |
5.21lb (2.4kg) average |
Life |
Minimum 20,000 insertion/withdrawal cycles |
Environmental |
|
Humidity |
To 95% (operating and non-operating) |
Moisture Resistance |
Per MIL-STD-202F, Method 106E |
Salt Spray |
Per MIL-STD-202F, Method 101D |
Temperature |
–40 to 149˚F (–40 to 65˚C) operating –67 to 185˚F (–55 to 85˚C) non-operating |
Thermal Shock |
Per MIL-STD-202F, Method 107D |
Figure 6-54 120 Ohms Converter Rear
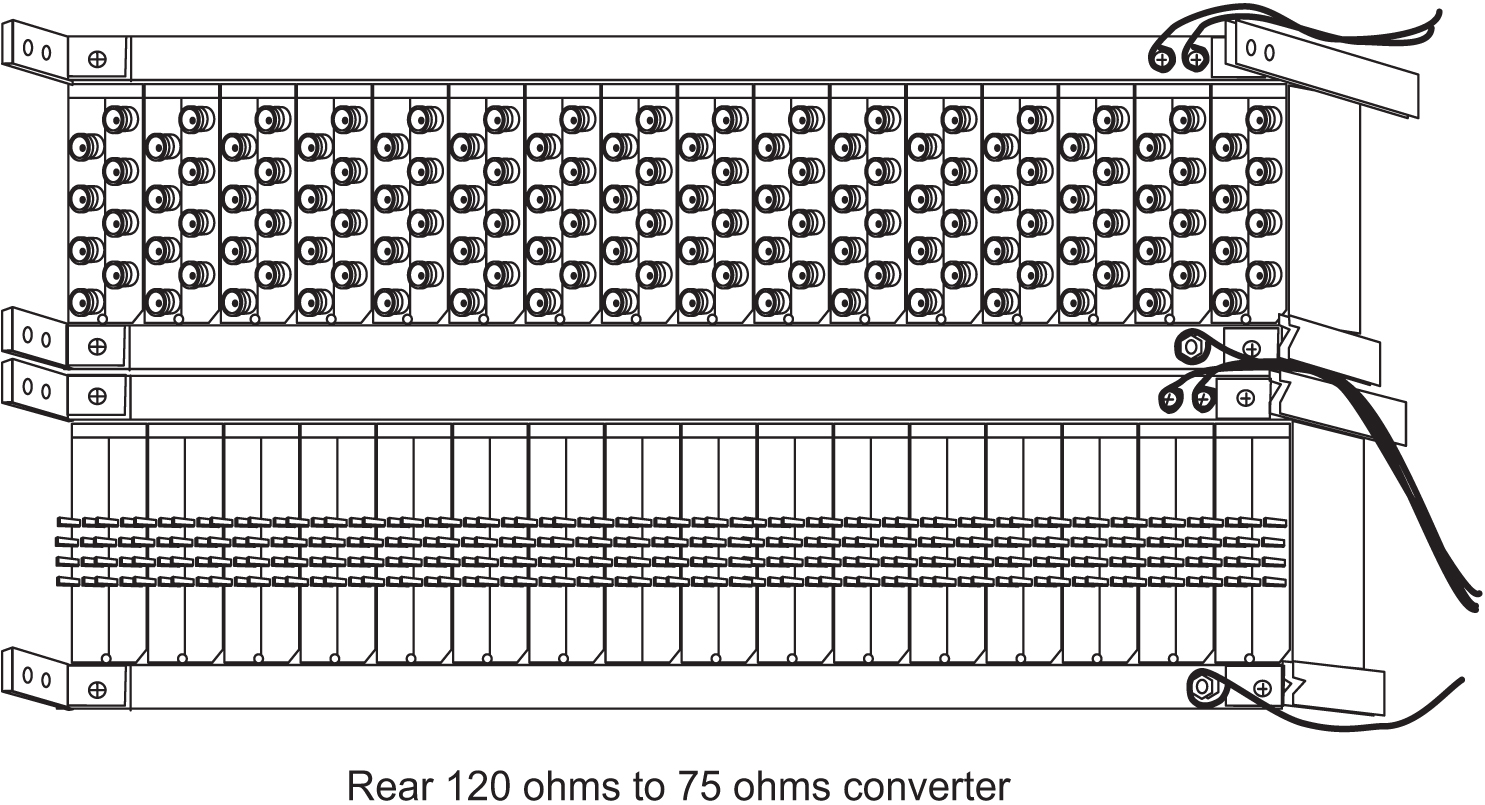
Figure 6-55 Converter Rear Detail
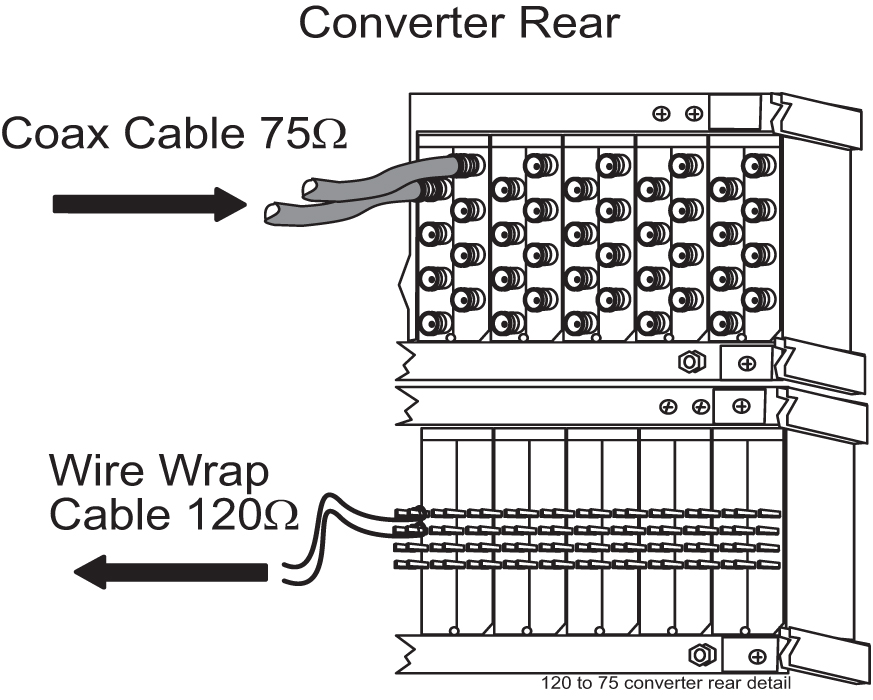
6.10 Hardware Acceptance
This section is intended for installation and test personnel. This section describes an inspection of the general system installation but does not attempt to cover testing of the system software.
danger:
No commercially AC powered equipment may be used or placed within 7 ft. of –48V equipment. This may create a shock or current loop that can be severely hazardous to personnel and equipment.Hardware operational testing is designed to verify the functionality of the finalized construction of the hardware at the customer site. The demarcation line for the testing is up to and including the patch panel directly connected to the system. The ability to route traffic through this system is verified using a Message Generator Traffic Simulator (MGTS). All cabling, alarm output, clock input, and other Oracle equipment is also verified operational per the Hardware Operational Test Manual provided with the test equipment.
Caution:
All personnel associated with the installation of this system must adhere to all safety precautions and use required protection equipment, to avoid the possibility of injury to personnel, service degradation, and/or service interruption.Caution:
This is a redundant system, to allow service during normal maintenance. When repairs require a total power disconnect, both input supply sources must be disconnected. This will cause service interruption and takes down the system.The customer frame layout is site specific, however the most typical frame layout is constructed with Extension Frames to the right of the Control Frame when viewed from the front. The OAP Frame is normally on the left of the Control Frame. Other frames (Miscellaneous and other support or feature specific frames) are lined up to the left of the Control Frame. General Inspection.
Procedure — Perform General Installation Inspection
Verify the following:
-
All items listed in the Equipment Specification have been installed.
-
Cabling is neatly installed and the labels are correct and easily readable.
-
Power cabling does not run through a cable rack.
-
Power cabling is not routed together with any other cables and has at least six inches of clearance.
-
Racks have Nomex paper between the rack and any power cables that would otherwise touch the rack.
-
The main central office ground is correctly labeled and has the “Do Not Remove” tag installed on the central office grounding bar. No “double lugs” are allowed. Any bolt through a nut must show at least two threads beyond the nut but no more than four threads should be showing.
-
The –48VDC power feeds are correctly labeled at the central office power distribution panel. There should be an A feed and a B feed for each frame.
-
The –48VDC returns are correctly labeled. There should be an A return and a B return for each frame.
-
Frames are level.
-
Earthquake bracing, if any, is properly installed.
-
Adequate floor clearances have been maintained.
-
Rear panels are installed.
-
Cable connections are tight at the backplane connections.
-
Cable sheets are properly marked and located in door pocket.
-
All documentation has been received and is available.
-
Terminals and printers connected to the system are operational.
-
Data cartridges have been received and are properly stored.
-
Any attached modems are operational.
-
Shipping container is properly packed with ramp and frame dollies prepared for shipment.
-
The area is clean and unused material has been properly disposed of.
6.11 –48VDC Power Source
This section verifies that the –48VDC Power Source has been labeled and connected correctly to the corresponding system frame's Fuse and Alarm Panels (FAPs). Your system may not include all of the frames described.
danger:
No commercially AC powered equipment may be used or placed within 7 ft. of –48V equipment. This may create a shock or current loop that can be severely hazardous to personnel and equipment.warning:
Do not carry exposed metal keys or tools in pockets or on belts when working on or around electronic equipment. Do not wear metal rings, watches, or jewelry on wrists or hands when working on any electronic equipment or other related electrostatic sensitive components. Always wear a wrist strap or other electrostatic protection when handling printed circuit cards and other electrostatic sensitive devices.warning:
Before beginning any of the following procedures, ensure that all breakers that provide power to the system are open.warning:
Before performing the following procedures do the following:-
Ensure that no power is being provided to the system from the –48VDC power source, such as a power board
-
Ensure that no circuit cards are installed in the shelves
-
Remove all fuses from the fuse and alarm panels
-
Recheck wiring and connections for proper polarity
Caution:
All personnel associated with the installation of this system must adhere to all safety precautions and use required protection equipment, to avoid the possibility of injury to personnel, service degradation, and/or service interruption.Caution:
This is a redundant system, to allow service during normal maintenance. When repairs require a total power disconnect, both input supply sources must be disconnected. This will cause service interruption and takes down the system.